ABOUT
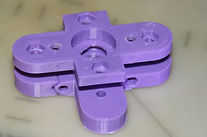
The Mk1 Hotend Piezo Z-Probe
Piezoelectric bimorphs are used extensively in industry for precision measuring and precision movement i.e. laser aiming. Their use in 3D printing has strangely been only a recent event. Beginning with the work of Njal Brekke, and then the follow up by Mike Simpson and Idris Nowell in 2016 they were successfully used to detect nozzle contact by being placed under the print bed. Later I realised that this could be simplified by drilling through the piezo disc and incorporating it into the hotend. This lead to extensive testing and development of the hotend mounted sensor which now uses 20mm piezo discs for a more compact unit.
​
Of all the other sensing technologies being used in 3D printing, we believe this one is the best at present. Nozzle contact is a direct measurement, the nozzle is the "sharp end of the tool". Since there are no x and y offsets (and very minimal z-offset) the whole of the printable area of the bed can be probed. It is permanently mounted so no servos to setup, and no issues with repeatability between probings. Any type of tilt in the carriage or effector does not result in probing errors being fed into computations for bed levelling or calibration.
​
If you use a delta printer there are designs for other effector-integrated piezoelectric units which might be suitable, although you can use Piezo20 units on a delta also, the screw mount version possibly works best.
More details about how piezoelectric sensors work and the principles behind them can be found here.
​
If you have any ideas/thoughts about piezo sensing technologies for 3D printing, we would be very interested in discussing it with you, join us at RepRap forum.
Happy printing.
​
​
Piezoelectric bimorphs are used extensively in industry for precision measuring and precision movement i.e. laser aiming. Their use in 3D printing has strangely been only a recent event. Beginning with the work of Njal Brekke, and then the follow up by Mike Simpson and Idris Nowell in 2016 they were successfully used to detect nozzle contact by being placed under the print bed. Later I realised that this could be simplified by drilling through the piezo disc and incorporating it into the hotend. This lead to extensive testing and development of the hotend mounted sensor which now uses 20mm piezo discs for a more compact unit.
​
Of all the other sensing technologies being used in 3D printing, we believe this one is the best at present. Nozzle contact is a direct measurement, the nozzle is the "sharp end of the tool". Since there are no x and y offsets (and very minimal z-offset) the whole of the printable area of the bed can be probed. It is permanently mounted so no servos to setup, and no issues with repeatability between probings. Any type of tilt in the carriage or effector does not result in probing errors being fed into computations for bed levelling or calibration.
​
If you use a delta printer there are designs for other effector-integrated piezoelectric units which might be suitable, although you can use Piezo20 units on a delta also, the screw mount version possibly works best.
More details about how piezoelectric sensors work and the principles behind them can be found here.
​
If you have any ideas/thoughts about piezo sensing technologies for 3D printing, we would be very interested in discussing it with you, join us at RepRap forum.
Happy printing.
​
​
TEAM
Simon Khoury
(DjDemonD)
I have been 3D-printing for 3 years now and have an interest in sensing technologies. I am doing this to give something back to 3D printing after benefiting from all of the wonderful ideas of others up until now.
Idris Nowell
(Moriquendi)
Idris has been instrumental in developing the piezo probing techology, and specialises in electronics.
The printed circuit boards that are the core of the system are Idris' hard work and ingenuity.
Mike Simpson
(Leadinglights)
Mike has been one of the key innovators in the use of piezo technology for 3D printing and acts as an advisor.
THE WORK
Currently, we divide out time between developing new ideas and fulfilling orders to our customers. Both Simon and Idris work at this as a part-time job, and have other interests.
Idris designs and manufactures the PCBs, Simon markets and fulfils the orders. We have some YouTube videos of what we do.
​
​